Within the current fast-paced manufacturing landscape, the pressure to produce high-quality products promptly and effectively has never been more intense. Firms across various industries are constantly seeking innovative solutions to streamline their production processes while upholding accuracy and cost-effectiveness. One particular solution gaining widespread attention is quick injection molding, a technique that which not only enhances manufacturing speed but also improves overall effectiveness in product development.
Rapid injection molding utilizes cutting-edge technologies and methodologies to shorten lead times significantly, enabling the swift production of complex designs and prototypes. This method not only accelerates time to market but also provides manufacturers with the flexibility to implement adjustments during development, ensuring that the final product satisfies exact specifications. As businesses continue to embrace rapid injection molding, they open up the possibility for faster innovation cycles and increased competitiveness in their respective markets.
Introduction of Rapid Injection Molding
Accelerated injectable forming is a state-of-the-art manufacturing process that optimizes product creation by substantially reducing lead times. This method utilizes innovative technologies and materials to produce top-notch plastic parts rapidly and effectively. Unlike classic injection molding, rapid injection molding utilizes prototype molds and enhanced production techniques to speed up the entire process, making it suitable for companies looking to expedite their time-to-market.
The core advantage of accelerated injection molding lies in its capability to create sophisticated geometries and intricate designs with precision. By using rapid prototyping methods, designers can test and improve on their concepts much more efficiently, allowing for prompt feedback and improvements. This agility not only saves time but also reduces costs associated with material waste and production delays, providing businesses with a market advantage in fast-paced industries.
Furthermore, rapid injection molding supports a diverse array of applications, from retail products to automobile parts. Manufacturers can produce small to medium-sized runs without the need for extensive tooling, making it a versatile solution for both emerging companies and established companies. The focus on speed and efficiency helps organizations react to market demands more efficiently, reinforcing the value of fast injection molding in the modern manufacturing landscape.
Advantages of Fast Injection Molding
Quick injection molding offers substantial time savings in the product development cycle. Traditional manufacturing methods often require lengthy lead times, but fast injection molding can accelerate this process. By utilizing cutting-edge techniques and technologies, manufacturers can produce premium molds swiftly, reducing the time from concept to market. This quickness allows companies to respond promptly to consumer demands and stay ahead of competitors.
Another essential advantage of rapid injection molding is cost efficiency. While initial investments in rapid tooling may appear high, the overall reductions come from lowered material waste and briefer production runs. This method is particularly valuable for producing tiny to moderate batches, where traditional metal tooling would be ineffective and costly. By minimizing material costs and enhancing production efficiency, companies can allocate resources in a better way.
Additionally, rapid injection molding supports design flexibility and innovation. The process allows for quick iterations of prototypes, enabling designers to evaluate and refine their concepts quickly. This encourages creative problem-solving and the exploration of new ideas, ultimately leading to superior end products. The ability to include feedback and make changes in actual time fosters a culture of continuous improvement in manufacturing, benefiting both producers and customers alike.
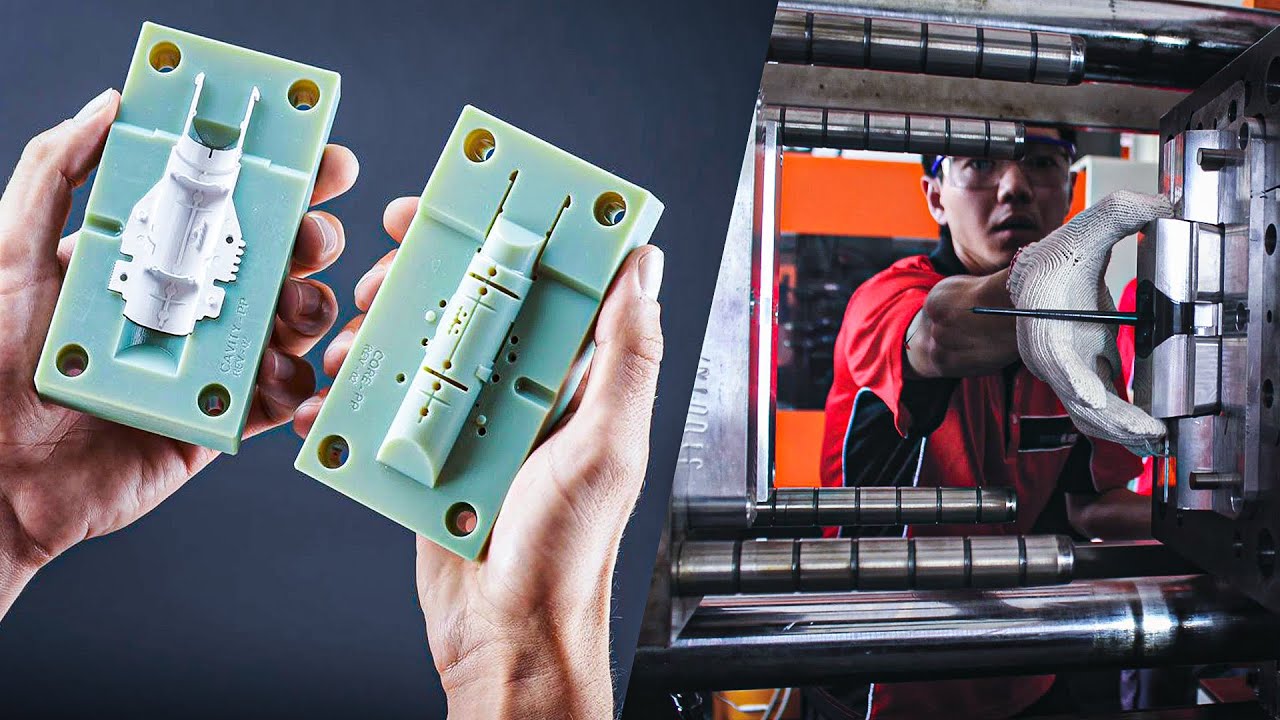
Utilizations and Illustrations
Fast injection molding has identified uses across different industries, enabling quicker product development phases and lowering costs. In the automotive sector, manufacturers utilize rapid injection molding to manufacture prototypes and production parts quickly. This technology allows for trialing of design and functionality, significantly minimizing the time to market. For instance, a top car manufacturer utilized this method to develop complex components, which were created and evaluated in days rather than months.
In the medical industry, rapid injection molding has a key role in the manufacturing of medical devices and components. The capacity to swiftly iterate designs based on government feedback is critical for continuing compliant and innovative. A specific instance showcased a medical device company that developed a new insulin injector using rapid injection molding, expediting the design phase and ensuring timely delivery to hospitals and clinics that quickly needed the product.
Personal electronics also profit from rapid injection molding as brands work to remain competitive through rapid product launches. A notable electronics company employed this technique to manufacture custom housings for their devices, enabling them to improve their designs based on consumer feedback. By leveraging rapid injection molding, they maintained a continuous pipeline of new products, adapting efficiently to market trends and consumer preferences.